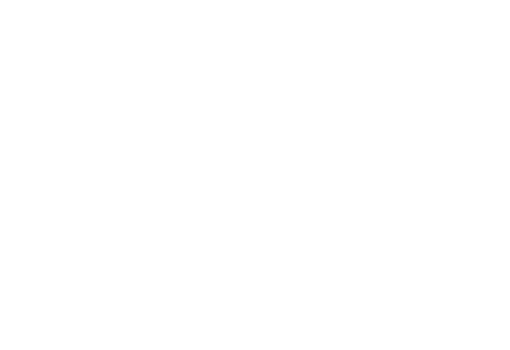
Our journey toward technological innovation began in Savannah, Georgia, with the launch of a transformative project in September 2022. By June 2023, we had implemented the automation phase at one of our two Savannah Distribution Centers, laying the foundation for the cutting-edge advancements we are now deploying across our operations. At the heart of these innovations are robotics and efficiency-driven processes, carefully designed to streamline our workflow.
The valuable insights and best practices we gained in Savannah have been seamlessly applied at our Toronto Distribution Center (DC), where, this fall, we proudly completed the final phase of integrating a sophisticated automation system. This milestone marks a significant leap forward, enhancing operational efficiency and precision. The new system is meticulously crafted to optimize processes, improve accuracy, elevate safety, and boost throughput, all while transforming the management, processing, and shipment of inventory.
Let’s now explore in greater detail the innovative updates that are reshaping the future of logistics at Anatolia’s Toronto DC.
Inbound Process: Precision at Every Step
At the heart of Anatolia’s operational advancement is the advanced inbound conveyor system, designed to provide 100% inventory accuracy. As pallets move along the conveyor, they undergo real-time checks for size, humidity, and weight. Any pallet that falls outside the predefined criteria, such as a damaged pallet or one with unstable products, is automatically rejected and rerouted for corrective action. This process not only ensures product integrity but also guarantees operational efficiency, handling a minimum of 1,400 inbound pallet placements daily.
Picking Process: Maximizing Productivity with Precision
Anatolia’s new picking process is a game-changer in terms of both speed and accuracy. Thanks to the integration of automation, operators can now pick up to 12 open pallets per hour—equivalent to approximately 42-line items—without the need to manually search for products. Robots seamlessly deliver pallets directly to the operators, ensuring that the right products are always in the right place at the right time. With weight control integrated into the system, each pick is meticulously checked for accuracy, reducing the risk of human error and optimizing overall productivity.
Vertical Storage Units (VSU): Space-Saving Efficiency
Space utilization is a critical factor in modern distribution centers, and Anatolia’s Toronto DC is no exception. The facility features two cutting-edge Vertical Storage Units (VSUs)—one dedicated to samples and the other to regular and courier orders. These advanced, automated piece-picking systems store items in a vertical cabinet-like arrangement, using vertical space rather than requiring operators to manually retrieve products from pallets. Instead, items are automatically retrieved at the touch of a button, significantly reducing time spent on order fulfillment and enhancing overall workflow efficiency.
Laser-Guided Vehicles (LGVs): The Future of Transport
Anatolia’s logistics operation is further enhanced by the deployment of 20 Laser-Guided Vehicles (LGVs), which execute up to 200 missions per hour. These autonomous vehicles, capable of stacking items up to 35 feet high, work around the clock, operating 24/7 with minimal downtime. With just a 5-minute charge, each LGV can function for up to an hour, making them highly efficient in managing the movement of goods within the facility. Equipped with advanced safety features, the LGVs ensure a smooth and secure flow of products, adding an additional layer of reliability to Anatolia’s operations.
Automated Wrapping: Speed and Security Combined
The wrapping process at Anatolia’s Toronto DC has been completely automated to enhance both speed and security. The smart wrapping machine efficiently secures products in seconds, with no human intervention required. This system ensures that every package is wrapped consistently and securely, ready for shipment with the utmost care.
Automatic Labeling: Streamlined Shipping for Maximum Efficiency
Anatolia’s commitment to automation extends to the labeling process as well. Shipment labels, embedded with RFID technology, are automatically printed and applied to open pallets, eliminating the need for manual scanning or label printing. This automated system streamlines the shipping process, reducing labor costs and the potential for human error, while ensuring the swift and accurate labeling of each shipment.
The Tangible Benefits of Automation
The integration of these advanced automation technologies represents a significant leap toward a more efficient, accurate, and scalable operational model at Anatolia. The reduction in human error and intervention allows staff to focus on higher-value tasks such as loading and unloading, while the system as a whole delivers greater inventory accuracy, faster throughput, and more timely shipments. As a result, Anatolia is not only improving its operational efficiency but also enhancing the overall customer experience, ensuring that products are delivered quickly and accurately, every time.
In conclusion, the Toronto DC’s new automation system is poised to redefine the standards of operational excellence in the distribution industry. With its blend of innovation, precision, and efficiency, Anatolia is setting the stage for a new era of logistics that will not only meet the demands of today but also pave the way for the future of supply chain management.
Anatolia is committed to expanding the implementation of these advanced solutions across all operations, continuously enhancing our technological systems and processes to further drive operational excellence and innovation.